History of Automated Guided Vehicles
Automated Guided Vehicles, which are basically driverless forklifts and other materials handling vehicles, were invented by A.M. Barret Jr. in 1953 when he took a modified towing tractor that had been used to pull a trailer and configured it to follow an overhead wire in a grocery warehouse, allowing the vehicle to be operated automatically.
Soon afterward, Barrett Electronics, of Northbrook, Illinois, began to market a rudimentary AGV, which was simply a tow truck that followed a wire that was embedded into the floor of a warehouse or factory. The technology soon proved to be appealing to factory and warehouse owners throughout the US during the late ’50s and early ’60s.
The Next Big Thing
The next big development came in 1973, when engineers at the Volvo auto assembly plant in Kalmar, Sweden, developed non-synchronous assembly equipment as an alternative to the traditional conveyor-centric assembly line. Eventually, 280 computer-controlled AGVs were installed in the warehouse. Volvo later marketed their unit load AGVs to other car companies.
Early model AGVs were guided using wires and tape, but today AGVs are mostly navigated using lasers. These type of vehicles, known as Laser Guided Vehicles (LGVs), are linked to other robots to ensure that products are moved efficiently throughout the warehouse.
Types of AGVs
There are three basic types of AGVs:
1. Driverless Trains – This is a towing vehicle that pulls one or more trailers to form a train. It is useful in moving heavy payloads over long distances without intermediate pickup or drop-off points along the route. The capacity of some driverless trains can reach 60,000 pounds.
2. AGV Pallet Trucks – These are pallet trucks that can move palletized loads along preprogrammed routes. Some can handle two pallets simultaneously and can use vertical controls to add or remove pallets from shelves or storage.
3. Unit Load Carriers – This type of AGV is used to move unit loads from one station to another and for automatic loading and unloading of pallets by means of rollers. They typically have lower payload capacity than other types of AGVs and are used for carrying smaller loads.
AGVs are used for raw materials handling, work-in-process movement, pallet handling, and finished product handling. They are used by many businesses because they can reduce labor costs, provide flexibility, save time, and can significantly reduce production and warehouse costs. They currently are used in many industries, including aerospace, food, and beverage, news printing, pharmaceuticals, warehousing, manufacturing, and mail processing.
AGVs are always being improved. A new development is AGVs that don’t use batteries.
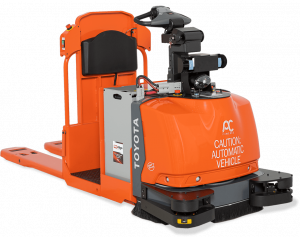
Image courtesy of Toyota Forklift – Bahrns ToyotaLift is an award-winning Toyota Forklift Dealership